Type of Breathable textile materials | Methods of producing Breathable textiles
Breathability refers to the ability of a fabric to absorb moisture and release it through the material itself, allowing it to ‘breathe’. Breathable Fabrics transmit body moisture away from the body, thus maximizing comfort and dryness during outdoor activities.
Waterproof Vs. Water Repellent Vs. Water Resistant
This looks above three terms are alike but there is a difference between waterproof, water repellent and water resistant. We must at the very beginning distinguish between “waterproof” and “water-repellent” textile surfaces. When you start to add breathability into the mix, things can start to get a little complicated. So, you should have clarified what do they all mean and why should you take note of the differences?
Definitions
Waterproof
- Waterproof fabrics are fabrics that are inherently or have been treated to become, resistant to penetration by water and wetting. The term “waterproof” refers to conformance to a governing specification and specific conditions of a laboratory test method.Even when you put pressure on a waterproof garment, it will still be impervious to water. The amount of pressure you can put on the garment before you start to get wet varies, and you can find out what that amount is by checking the garment’s water column.
Water Repellent
Water-repellent treatment is a standard finishing process for modern textiles in order to create breathable textiles. Water-repellent agents exploit the high-water repellency of silicones without impairing the textiles’ ability to breathe. Additionally, they confer a soft hand on textiles.
Water repellency is, therefore, a step up from water resistance. This means that water can’t easily penetrate the material (the technical term is that it’s hydrophobic).
Meaning:
- Not easily penetrated by water, especially as a result of being treated for such a purpose with a surface coating. It beads on the outside instead. The fabric is a densely woven and it offers some water resistance.
- Adjective (of fabrics, garments, etc) having a finish that resists the absorption of water
- Adjective having a finish that resists but is not impervious to water.
- Water-repellent clothing or material does not absorb water when it is raining lightly
- Able to keep rain from being absorbed.
Water Resistant
This offers the lowest level of water protection. If a garment resists water, it’s usually because the fabric itself is acting as a barrier between you and a light shower. Tightly woven fabrics will offer a degree of water resistance, as it takes some time for the water to seep through the material.
Adjective
- Able to resist the penetration of water to some degree but not entirely
- Resisting though not entirely prevent the penetration of water.
The Definition of Breathability
In a nutshell, breathability refers to the ability of a fabric to absorb moisture and release it through the material itself, allowing it to ‘breathe’. Breathable means that a fabric permits perspiration vapors to escape from the body through the fabric. During strenuous activity, the body releases moisture vapors, and the skin breathes this moisture as it naturally tries to cool itself down.
Breathable Fabrics transmit body moisture away from the body, thus maximizing comfort and dryness during outdoor activities. This continuous cycle of motion is at the heart of the mechanism of breathability: the more you sweat inside a breathable clothing item, the higher its perspiring capacity should be, and this circular action never stops.
Breathability does not, as the term might imply, relate to an exchange of air. Instead, it is the ability of a fabric to allow moisture vapor to pass through it. A fabric may carry this out in numerous different ways, and exchange of air is only one possible avenue. Moisture vapor permeability (MVP) and moisture vapor transmission (MVT) are perhaps better, and certainly more technical, terms to use than breathability. Neither ASTM nor the Textile Institute defines breathability, but MVP and MVT are both defined in test standards.
Air permeability is intrinsically linked to breathability. Air permeability is “the velocity of an air flow passing perpendicularly through a test specimen under specified conditions of the test area, pressure drop, and time” (according to BS EN ISO 9237: 1995). All air permeable fabrics are breathable to some extent, though not all breathable fabrics are air permeable.
Application of durable water-repellent finishes by coating methods
Measuring the surface tension of the liquid, one may calculate the work of adhesion between the liquid and the surface of the solid. It is clear that the smaller the work of adhesion, the smaller will be the wettability and the greater will be the repellency.
What is water repellent finish?
The durability of Water-Repellent Finishes
Durable water repellent, or DWR, is a coating added to fabrics at the factory to make them water-resistant (or hydrophobic). Durable water repellents are commonly used in conjunction with waterproof breathable fabrics such as Gore-Tex to prevent the outer layer of fabric from becoming saturated with water.
A durable water repellent (DWR) is a functional finish for fabrics, which adds water-shedding properties to existing products. Garments treated with a DWR bead water droplets and force water to roll off the surface of the fabric.
The DWR, as the name suggests, repels water, i.e. water droplets form on the outer surface (as we stated above). And this plays an important role in breathability. When we say a jacket is “breathable”, we don’t actually mean it breathes. What we really mean is that it transports moisture – sweat – from the inside to the outside of the jacket.
For moisture to move from the inside to the outside but not the other way around, the face fabric can’t be soaked in water. As we stated above, hydrophilic fabrics on their own keep you dry from rain from the outside – as they soak it up – but they won’t keep you dry from your own sweat from the inside. So, it’s the combination of a hydrophilic material and a DWR that makes a jacket waterproof and breathable.
Hydrophilic fabrics are also impregnated with a durable water repellent (DWR). But if they inherently stop water reaching your skin, why do you need a DWR? Good question!
We did say this would get a little complicated! But what you need to take away from this is:
- Waterproofness is what you need to look for if you plan on wearing your gear in rainy or snowy conditions
- Breathability – i.e. transporting your sweat away from your skin – usually goes hand-in-hand with waterproofness
- Water repellency offers light rain resistance thanks to the impregnation
- Types of DWR Solutions
- Fluorine-free
- Fluorine-free DWR solutions are the future of water-repellency in the textile industry. These solutions contain no fluorochemicals, making them ultimate environmentally-friendly solutions for garments requiring water repellency.
- C8/C6: This solution is a chemical compound made up of carbon and fluorine atoms. These atoms form a long chain (C8), which helps repel water and oil from fabrics. Due to concerns from the Environmental Protection Agency (EPA) on fluorochemicals, mostly concerning toxicity and human contact, textile manufacturers have moved away from incorporating this technology into their garments. The fundamental difference between the C6 solutions and C8 is that the C6 solution contains fewer fluorochemicals, reducing the hazardous risk.
How DWRs Work
DWRs work by increasing the “contact angle” or “surface tension” created when water contacts a textile. Basically, a high contact angle creates a microscopically “spiky” surface that suspends water droplets on the outer fringe of the fabric.

An optimized DWR keeps droplets in a rounded shape—like a dome-shaped bead. The rounder the droplet, the easier it rolls off the fabric. A low contact angle permits droplets to assume a flattering shape, one that can spread out like a splotch, cling to the fabric’s surface and eventually seep into it.
DWR Ratings
Manufacturers generally measure DWR effectiveness by a spray test. Water is sprayed onto a textile, and the amount that sticks is visually assessed. A score of 90 points indicated that roughly 90% of the fabric has no water sticking to it. The higher the number, the better the performance. The test is then repeated after a number of washings to determine durability.
Test scores and the number of washings is combined to create a rating. For example, a 90/10 rating means the spray test achieved a total of 90 points after 10 washes.
Not all manufacturers publish DWR performance ratings, but here is a basic guide for interpreting any that you find:
- Good: 80 points after 10 washes. This is a basic outerwear finish.
- Excellent: 80 points after 20 washes. Marmot, for example, uses this as its minimum rating for outerwear.
- Superior: 80 points after 50 to 100 washes.
Fabric Production process and coating techniques
Fabric requirements need tendency of to resist wetting is a function of the chemical nature of the solid surface, the roughness of the surface, the porosity of the surface, and the presence of other molecules on the surface. Woven fabrics for water repellent/ water resistant/breathable textiles feature permeable pore channels between yarn interlocking points (mesopores), which create an increased risk of penetration by contaminated fluids and particles. These pore channels can be reduced in size by finer count and high-density weaving.

This, however, results in deteriorated drapability and performance characteristics. The barrier properties of the woven fabric are determined by the construction-dependent pore morphology (mesopores and micropores), and the surface character of the textile structures.

When used for protective garments, it is equally important to guarantee high wearing comfort. Fulfilling these conflicting requirements (barrier effect and comfort) in a single textile structure is an immense challenge. To impede the penetration or pervasion of fluids, barrier textiles are finished with fluorocarbon (FC) resin.
The hydrophilizing by means of FC also reduces the adsorption of water on the fibers. Such woven fabrics only have an effective barrier function against fluids at small amounts of fluid, low pressures, and short exposure times. In the simplest case (sieve effect), the maximum pore sizes present in the woven fabric determines particle retention. In the case of smaller particles and larger pores, further barrier mechanisms are known, such as retention by bridging and by adhesive forces (van der Waals forces), or by electrostatic forces.
In microfilament woven fabrics, deep-bed filtration also plays an important role. Particles penetrating into the woven fabric interact with the filament surfaces and can be deposited between the woven fabric filaments. In order to fully exploit the advantages of woven fabrics as barrier textiles (good drapability, high wearing comfort), mesopores present primarily at the crossing points of warp and weft yarns in the woven fabric are to be reduced in size by a targeted finishing with fine microparticles so that the woven fabric meets the stated requirements.
Coating Methods
Knife Coating (floating knife) or Direct Coating
In Knife Coating, as seen in Figure 3, the liquid coating is applied to the fabric while being run at tension under a floating knife blade, the distance between the fabric and the knife blade determines the thickness of the coating. The blade can be angled and have different profiles to affect the coverage. For this process to be effective the liquid coating must be quite viscous in order to prevent it from soaking through the fabric, the coating is then dried or cured.This technique is best used for Filament yarns as the staple fibers in spun yarns can protrude on the surface creating an uneven finish, but this is dependent upon the thickness of the applied coating. For this type of coating to be most successful the weave structure has to be quite tight and the fabric capable of being held taught.Figure 3. Fung, W, 2002, Coated and Laminated Textiles, UK; Woodhead Publishing; Direct Roll Coating
In this process, the coating liquid is rolled onto the fabric by a roller suspended in the coating solution, often a blade is positioned close to the roller to ensure not too much coating solution is applied.Figure 4. Direct Roll Coating from;Sen, A K, 2008, Coated Textiles; Principles and Applications, 2nd Edition, USA;Taylor and Francis. Pad-Dry-Cure
Also referred to as Padding, this technique, widely regarded as a textile finishing technique, can, in fact, be used to add a variety of coatings, but this usually refers to a fiber coating for the application of micro or nanomaterials or chemical compositions.As shown in figure 5, the fabric is submerged in the coating solution then the excess squeezed out in the rollers, which dictates the pick-up percentage, the fabric is then dried and cured.Figure 5 Calender coating
Calender finishing involves the fabric passing through a set of heated rollers to singe off any surface fibers and add lustre and smoothness. Calender coating is the same principle in which the fabric passes through heated rollers, but through this process, a coating is applied as demonstrated in figure 6. This image demonstrates the simultaneous coating of both sides of the fabric with the thickness of the coating determined by the width of the nip in-between the rollers, more rollers used can provide a thinner coating.Figure 6. Depicts calender coating. Image from; TPO coated PP fabrics and their applications Hot melt extrusion coating
Hot melt extrusion coating is applied in the same process as calendaring with the coating being melted from granules fed to heated rollers which then nip the coating to the fabric. It is used to produce un-supported films and these freshly produced films are added directly to the fabric. Its uses are mainly for Thermoplastic polymers such as Polyurethane, Polyolefins, and PVC.Foam Finishing
Foam finishing was developed as a more environmentally friendly version of the pad-dry-cure system, as the chemical applied requires less product in weight, but equates to a high surface area. Foam also ensures lesser wetting takes place, which requires less drying; furthermore, waste is reduced in terms of residual liquor. This technique is useful in coating heavy fabrics such as carpets and can be used to effectively coat only one side.
Test Method of Specified Requirements of Water Repellency Textiles
Water Repellent Textiles
Water repellent fabrics are processed with water repellent additives so that water droplets form on the surface but do not penetrate the fabric, a phenomenon known as “the lotus effect.” The efficiency of water repellency is graded in 6 ratings as 0, 50, 70, 80, 90 and 100. A standard test is usually performed after five launderings with water at a temperature of forty degrees Celsius. To qualify as water repellent, the fabric must perform to at least rating four (90% or better efficiency). Further tests for the endurance of water repellency may be performed after 20, 50 or 100 launderings at similar temperatures to the initial test. Water Repellency Textiles are commonly used in fabrics for windbreakers outer garments, umbrellas, furniture decorations to name just a few.
Taiwan technology for Water Repellent Textiles achieves rating 100 initially, and not less than rating 80 after 100 launderings. The test method employed is AATCC 22. The Optical Contact Angle for lotus leaf is 135°; ordinary water-repellency treatments reach 130°; ordinary nano-treatments achieve 140°. However, with Taiwan’s special nano-technology for functional textiles, the Optical Contact Angle reaches up to 150°.
Scope
This criterion defines the evaluation and testing of water repellency textiles. It is applicable to textiles with
water-repellent finishes. However, it is not intended to measure penetration of water through the textiles.Terminology
Water repellency: the characteristic of textile to resist surface wetting.Performance specification
Grade classification
100(ISO 5) Excellent
90(ISO 4) Very Good
80(ISO 3) Good
70(ISO 2) —
50(ISO 1) —
0 —Test Method
Water RepellencyTest Specimens
Three test specimens 180.0×180.0mm are needed and should be conditioned at 65+/-2% relative humidity and 20+/-2°C until moisture equilibrium.Test Procedure
- Fasten the test specimen securely in the 150+/-5 mm diameter hoop so that the face of the test specimen will be exposed to the water spray. The surface of the specimen should be smooth and without wrinkles. Place the hoop on the stand of the tester in 45° with the specimen uppermost in such a position that center of the spray pattern
coincides with the center of the hoop. The distance should be 150+/-2 mm. Make sure that the warp direction of the test specimen should parallel to the watering direction. - Pour 250ml of distilled water into the funnel of the tester and allow it to spray onto the test specimen for 25 to 30 seconds. Take the hoop by the bottom edge and tap the opposite edge firmly once against a solid object with the fabric facing the object, then rotate the hoop 180° and tap once more on the point previously held.
- Repeat the procedure above for other 2 specimens.
- Evaluation and Report After tapping, immediately compare the wet or spotted pattern with the rating chart. Rate the face of the specimen. Report the worst rating.
- Washing requirement: Select the specified washing condition and drying method based on the suppliers’ provided care instruction.
- Fill the washing machine with water to 18Gal (about 68L) and adjust the water temperature. Machine Cycle Washing Temperature Drying Procedure (1) Normal/Cotton Sturdy (2) Delicate (3) Permanent Press (II) 27+/-3°C
(80+/-5°F) (III) 41+/-3°C (105+/-5°F) (IV) 49+/-3°C (120+/-5°F) (V) 60+/-3°C (140+/-5°F) (A) Tumble i. Cotton Sturdy ii. Delicate iii. Permanent Press (B) Line (C) Drip (D) Screen - Add 66+/-1g of 1993 AATCC Standard Reference Detergent to the washing machine. Then, add the test specimens and ballast (total weight: 1.8+/-0.1kg) into the machine. Set the washer for the selected washing cycle and time.
- Remove the specimen after the final spin and dry the specimen according to the specified method. After drying, condition the specimens by laying each specimen separately on the screen in an atmosphere of 20+/-2°C and 65+/-2%
RH. until it achieves moisture equilibrium.
- Fasten the test specimen securely in the 150+/-5 mm diameter hoop so that the face of the test specimen will be exposed to the water spray. The surface of the specimen should be smooth and without wrinkles. Place the hoop on the stand of the tester in 45° with the specimen uppermost in such a position that center of the spray pattern
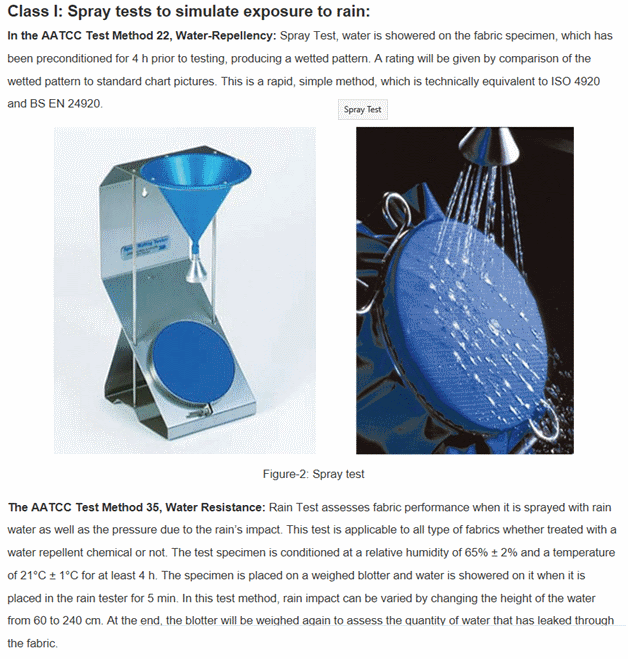
Summary and Conclusions
The theory of water repellency of textile fabrics has been reviewed with special references to the more recent theory of the wetting of fabrics by water. A survey has also been made on the various testing methods that have been devised for measuring water repellency. The results of the present investigation lead to the following conclusions regarding the status of water repellency. There is a definite need for a comprehensive study of the role that the structure of a fabric plays in the phenomena of water repellency. Students can take these projects and develop the products in their workshops, chemical laborite and test them in the testing laboratory.
In the past, the emphasis has been on developing more efficient compounds. Data available indicate that a better understanding of fabric construction as it applies to repellency, coupled with the now available water-repellent agents, will lead to some more nearly idealized type of water-repellent garment. In regard to testing methods, it is required that correlation is established between the Water-Repellent Fabrics results of laboratory test methods and performance of fabrics.
As already stated, the contact angle is influenced by the following factors: The’ chemical nature of the solid surface, the porosity of the surface, and the presence of other molecules on the surface. Again, any one or all of these factors could diminish the contact angle during wetting of the fabric. The change will indicate moisture regain of the sample which will show that the rate at which a fabric absorbs moisture increases the proportion to the number of times the sample has been wetted. It is of interest to re-exam the surface factors that might be responsible for the increase in moisture absorption.
The loss in the repellent agent, the change in position of the fibers in the yarns, and the creation of new surface could all affect the rate of water absorption. The swelling of partially coated or uncoated fibers would also result to make available more hydrophilic surfaces (OH groups). Now, a team at MIT has come up with a promising solution: a coating that not only adds water-repellency to natural fabrics such as cotton and silk but is also more effective than the existing coatings.
The new findings are described in the journal Advanced Functional Materials, in a paper by MIT professors Kripa Varanasi and Karen Gleason, former MIT postdoc Dan Soto, and two others.
Closing Remarks
Now that you know that “water-repellent” is a characteristic, and understand the differences between water-resistance and waterproofness in fabrics, you should have a newfound sense of reassured confidence when purchasing the perfect product that meets your needs. Being mindful of label descriptions can greatly assist you in deciding whether a product will be suitable for the conditions that you expose it to.
No comments:
Post a Comment